Keeping the human factor present in digital factories
- 6 September 2021
- Posted by: Iris ten Have
- Category: IFFI's column in Evmi
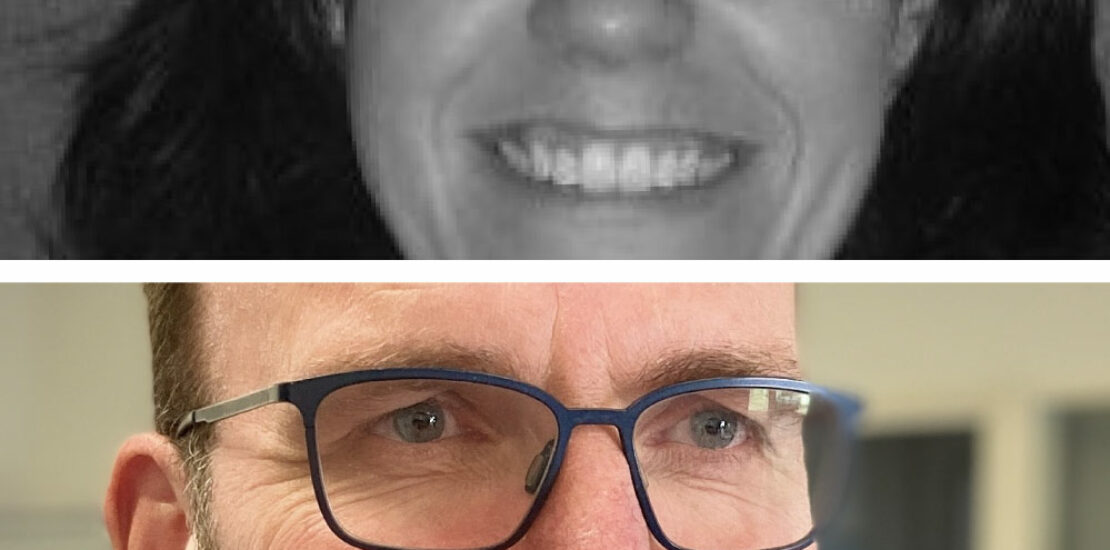
Digital factories – it is the topic of IFFI’s upcoming masterclass. With rapidly evolving digitalization and the interconnectedness of systems, it is important for factory processes to keep up the pace. Manager Technology Hilde van der Ploeg and Senior Process Technologist Ronald Jansen will share insights on the digital transition of FrieslandCampina.
“Since the digital transition, which started around the fifties, there has been a general worry that digitalization would take over human jobs,” states Ronald. “However, machines can never replace human jobs entirely: where automation takes over jobs, other jobs are made possible on a societal level Digitalization also enables to make people’s work more humane. Use people where they are most powerful – not for routine work.”
In what way does your company profit from the digital transition?
“In the factory, the general goal is always to ensure that all factory processes are running as optimal as possible, meaning: creating the highest output possible, of the highest quality, and in a way that is as economically and environmentally sustainable as can be. “In the factory, we produce a lot of data. The moment you start to bring together data in a smart way, you achieve information. With that gathered information, it becomes possible to improve matters, gain insights, reveal processes that are not efficient. Based on this information, you can improve the processes in your factory.” Hilde van der Ploeg states. This is precisely what digitalization is useful for in the food industry.
“Digitalization makes the process more precise, and, on a cruder note, it also saves money in the long run. We produce milk for infants and we want the milk to resemble breastmilk as much as possible. We add components like vitamins to this milk so it has qualities as similar as possible to real breastmilk. It is crucial for the dosages to be exact, for if there is too much or too little of a certain ingredient in the milk, it may jeopardize the baby’s health. Digitizing this process ensures a more precise and safe conduct.
It enables us to create transparency between us and the customer. For instance, we have developed a QR-code to be printed on the packaging of our baby products. When the customer scans this with their phone, they can trace the product back to where it came from. This is possible thanks to our era of digitalization, where all information is stored. We can trace back the product to all the steps, from beginning to end.”
What is the main take-away from this dinner meeting?
“What we want to explain and convey with this dinner meeting, is actually how digitizing processes alleviates people from carrying out routine-like, repetitive daily tasks. Use people for their strengths and digitize the tasks that a robot or computer could perform better. The human factor should not disappear from factory work. Spontaneity and an open mind to change are necessary in the factory. People have those qualities, digital systems don’t. The idea is that both digital processes and people perform in their strengths.”
Why should people working in the food industry join this dinner meeting?
“First Wouter Schotborgh holds a lecture. We will make a link with the information he shares by describing what an operator can do the moment he or she notices a deviation in the digital process. How to use people at its best in the factory versus how to put automatic systems with generated data to their best use?
In the masterclass we will focus mainly on how to approach factory processes in relation to digitalization. How do you make use of your employees? How do you make use of digitalization?
Members can learn from our lecture and experiences, and so will we. They might discover new ways of digitalizing that they can apply to their own organization, and so may we get inspired by the shared experiences of our members.”